Quality Assurance
an excellent new fit-out.
Gregory Quality Systems
Gregory has been ISO9001 third party Quality Certified for many years, with robust processes and procedure to ensure that your fit-out projects run on time and on Budget. Gregory is also ISO14001 Sustainability Certified and has an ISO 45001 ready OHS program that we customise for each major installation program to work with your Builder’s requirements.
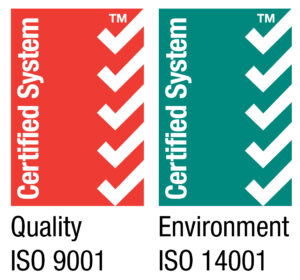
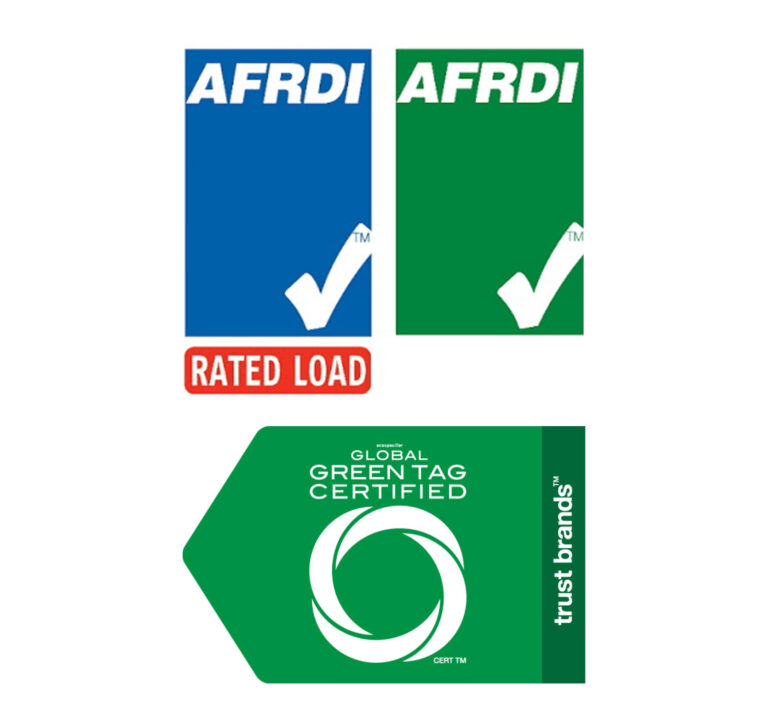
Sustainability and Durability
Our design processes, materials and component selection and our manufacturing are driven by our ISO9001 Quality and ISO14001 Sustainability processes to ensure you receive a best in class product. Most of our seating is AFRDI Certified to ensure maximum durability and long life. We lead in sustainability. Our Workstations include Greentag Certified options and our local Australian made seating is Greentick Certified. Sustainability has always been a key focus for Gregory from Product design to post use waste conversion and minimisation.
Many imported products have fantastic sustainability stories in their home markets but none of this backup infrastructure is in place in Australia as these products are imported in smaller quantities and without attention to these practices that exist at their point of origin.
Our programs include taking back the old desks from our clients and converting this waste material into the framework for our lounges and ottomans, giving the opportunity to divert 100’s of tonnes of materials from landfill.
Our takeback and recycling program is available on all Australian made task seating.This makes us the most sustainable commercial furniture provider in Australia.
Safety on site
A safe workplace is vital for our people and our customers. Gregory has a comprehensive approach to on-site safety management that is compliant with ISO45001 (download template document) that has been developed with the assistance of major builder Lendlease. This program includes daily site safely, Inspection and training protocols, risk and injury management plans and reporting. Installation programming is the key to a perfect job, because it’s important the our Quality processes extend outside the confines of a controlled factory environment onto the worksite and your premises. Our project installation teams are part of our QA system. Major projects can have a customised ISO 45001 compliant OHS program than also can me modified or tailored to suit the customer or builders own site OHS system. Our staff contracts are compliant with the requirements of the Building Code for work on Commonwealth and State projects and compliant with the National Code of Practice for the Construction Industry. Gregory is set up with Aconex, Hammertech, Oracle, Payapps, Estimate One, Science Warehouse and other construction industry management systems Our insurances include $50m Public and Product Liability coverage and also $5m Professional Indemnity Insurance. Individual State bases Workers Compensation Policies are in place in each State to cover our workers.
On-site management systems
On major multi day projects, full site reporting and QA photography recording and verification is available
Process Controls for a Quality Project... on time
All design, ordering, production, installation, clean up and warranty are managed within our Odoo Project management systems which are fully integrated with our records management and QA and accounting modules. These are managed to comply with Privacy and Security requirements. Our Project management workflow system uses backward scheduling to ensure that all work is programmed for manufacture and installation based on the committed project completion dates. We also actively work with your trades and builders to accommodate any of their unexpected overruns.
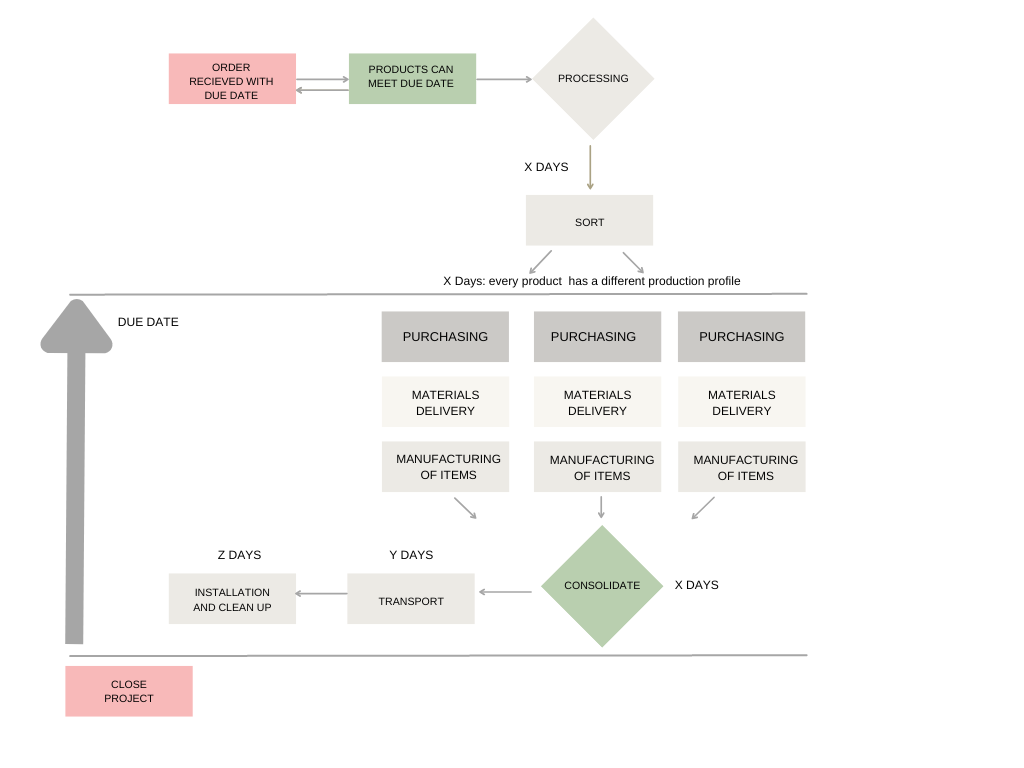
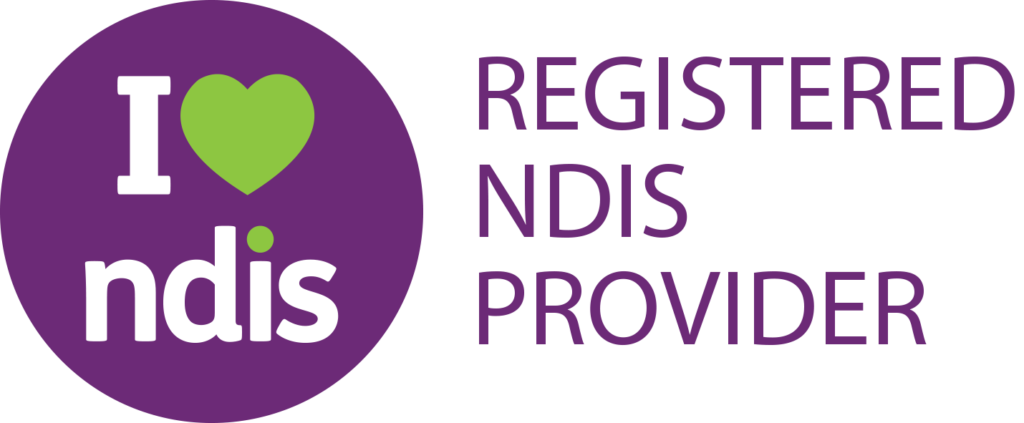
Registered NDIS Provider
Gregory Chairs is proud to be a registered NDIS provider, with the skills to provide specialist medical and infection control seating and specialized custom seating manufacture for Physiotherapist, Ergonomists and Health professionals who need specially made seating for their clients. This customised seating uses Gregory’s manufacturing skills and specialised materials and foams to produce quality, durable locally made seating for those with special needs and in particular back and sitting needs. This is a specialised Healthcare provider service and the instructions on particular seat manufacture and design need to come to us from your healthcare provider as we are not medically certified to provide this level of advice. In Hospital and Medical environments, Gregory provide outstanding staff and patient seating, designs that minimise detritus and Infection risks through our industry leading knowledge and advanced materials and construction. We are particularly aware of long term patient seating comfort and Circulation Our waiting room systems are designed to be easily maintained to ensure that the patient, whilst under stress is in a good environment and this reduces the risk of adverse staff interactions Mental health seating can be either permanently affixed or weighted to reduce injury issues.